Proses Validasyonu
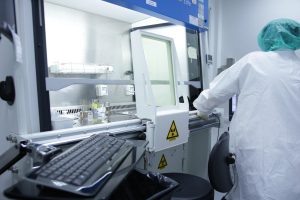
Process Validation is performed to ensure consistent delivery of quality products that meet predetermined specifications/requirements and quality specifications. This ensures the full safety and effectiveness of the medical device.
Our firm provides complete expertise in process validation and helps medical device manufacturers consistently meet required parameters through optimized manufacturing processes.
Equipment Qualification
IQ is the task of proving that equipment is suitable for its intended use.
Requirements for equipment are carefully determined, taking into account use and functionality.
In a lifecycle approach to process validation, using risk-based decision making throughout this lifecycle helps identify critical process parameters throughout the lifecycle as opposed to just specific phases of the process.
The qualification plan should consider usage requirements and may include risk management to prioritize certain activities and to determine a level of effort in both the performance and certification of qualification activities.
Medical Device Software Validation
Software Validation and Validation (Software V&V) is an integral part of software design, covering all development stages as specified in IEC 62304, which addresses the Software Development Lifecycle (SDLC) of medical software and software embedded in medical devices. Software Validation is testing whether the software is designed according to the requirements. Medical Device Software Verification tests whether the right product is made for the user.
Initially, the software is classified based on the level of concern based on both FDA guidance and the MDR’s classification rule. The classification may differ from one software subsystem in the architecture to the next, depending on the intended use of the software subsystem and the risks associated with it. This classification determines the documents that must be submitted to the regulatory body.
Medical Device Software Validation includes unit testing, software integration testing, software architecture validation, code-based static analysis, requirements-based software system validation, software regression testing, and software validation.
According to IEC 62304, the basic assumption is that medical device software is developed and maintained within risk management systems established by the manufacturer according to ISO 14971, with some minor additions to the software. All risks posed by the software, including data security, network security, and cybersecurity, must be identified, analyzed and mitigated so that all patient safety risks are addressed to ensure proper device performance.
Sterilization Validation
Sterilization of medical devices is of great importance in the medical device industry. The Medical Device Regulation, especially ISO 13485:2016, and then the Medical Device Regulation also attached great importance to sterilization.
With sterilization validation, the safety of the product is proven. The release of the product, which has been exposed to an unvalidated sterilization process, also brings risks. It can cause the surgeon to perform an additional operation on the patient, or even cause infections that can lead to death. The sterilization process kills the microorganisms on the product and eliminates the contamination, thus preventing the transfer of microorganisms and bacteria to the patient and infection.
It is the verification of the sterilization process according to the determined application standard and the provision of process safety.
During the validation services, it not only reports all of the IQ, OQ, PQ studies in accordance with the decided method, but also provides the necessary test studies.
Sterilization validation studies of medical devices are performed for all processes, including gamma radiation, ethylene oxide gas sterilization, hydrogen peroxide sterilization.
It operates within the scope of the following standards in sterilization and process validation.
- EN 11135:2014 Ethylene Oxide Sterilization Validation and Routine Controls
- EN 11137-1:2015 Radiation Sterilization Validation and Routine Controls
- EN 14937:2009 Identification, Validation and Routine Controls of General Characteristics of the Sterile Agent
- EN 17665-1:2006 Steam Autoclave Sterilization Validation Study
Test Method Validation
The purpose of method validation is to test that the chosen method yields results in accordance with the desired purpose (performance, quality) and to determine and control the conditions for providing the desired performance during routine use of the method. The application performance of the analysis method in chemical analysis depends on many factors. Therefore, the measurement method must be well defined. Depending on the sample analyzed, the type and amount of the analyzed components, it may be necessary to use different methods. Which of many different methods to use for a particular analysis should be determined as a result of an evaluation to be made depending on the type of sample analyzed, the amount of components to be analyzed, the number of analyzes to be performed daily, the quality of the desired result, the ease of application of the method, the analysis time, and the cost of the analysis.
Packaging Validation
Medical devices that are distributed sterile must be validated to be sterile and remain sterile until the sterile barrier system is damaged or opened. The most critical point for a sterile medical device is to ensure that sterility is maintained.
In order to meet the basic requirements of the European Medical Device Directives and to ensure product safety, packaging process validation studies must be carried out and documented in accordance with ISO 11607 and related test standards.
Medical Device Cleaning Validation
When it comes to the use of Reusable Medical Devices, the issues regarding the use of these devices have been specified together with the MDR regulation, and it has been stated that the procedures of disinfection and sterilization processes, especially cleaning, should be prepared and validated by the manufacturer.
Post-reuse cleaning methods of reusable medical devices are validated through the validation process. It is the responsibility of our manufacturers to define the cleaning and sterilization processes of reusable medical devices.
Cleaning of orthopedic implants is an important step to achieve their biocompatibility as well as controlling the microbiological load required for sterilization processes.
Implants can be delivered to the user sterile or non-sterile. In either case, it is the manufacturer’s responsibility to provide implants that have been cleaned to remove contaminating manufacturing materials.
The purpose of cleaning validation is to verify the effectiveness of the cleaning process in reducing physical, chemical and microbial contaminants below a defined level. Cleaning validation studies are carried out according to the ISO 19227 standard.